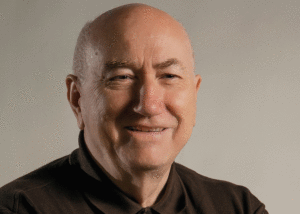
A material that today can be a valid alternative to plastic reinforced by fibReglass or anyway complementary in various areas of the boat, maybe soon for hulls, too. Interesting the process and the mix with other composites. we had the lucky opportunity to interview one of the most expert chemists in our sector: Ezio Businaro.
What types of composites are today available on the market?
Composites are various, depending on the used materials, the processes with which they are implemented and how they are designed in view of the final product-good.
The composite initially used and widely diffused in shipbuilding is plastic reinforced by fibreglass (in jargon), i.e. unsaturated polyester matrices and fibreglass reinforcements. The most used alternative is the composite with epoxy resin matrix and carbon fibre reinforcements. Generically, these two families of composites have offered two levels of performances to boat designers. They exist and have been used also alternative reinforcements made of aramid, basalt, and hybrids in glass-carbon and glass-aramid fibres. Today engineers’ interest is aroused by vegetal fibres (bio-reinforcements) and biopolymers (matrices) and, last but not least, thermoplastic matrices instead of the already mentioned thermosetting ones (resins).
Concerning processes, it is worth reminding the conventional one, the Hand Lay Up, and those introduced more recently in shipbuilding yards, grouped under the word Infusion. The boat building generally occurs at environmental temperatures (therefore with adequate chemistry), but, especially for race boats, with the aid of high temperatures and in autoclave, using for instance prepregs, generally in carbon-epoxy). Finally, we should also underline that in the design and manufacturing it is possible to provide for compact composites and sandwich composites.
What are the characteristics of composite vessels?
Generally, the properties of composite vessels are lightness, shape versatility and then wide range of final product-good, shorter implementation times and, as final outcome, lower building costs.
Why can plastic reinforced with fibreglass be problematic?
The problem of the chemical risk – release of styrene into the environment – for shipyard operators is still partially unsolved, despite suction plants (not always adequate) and personal protections (not always adopted). I would like to stress also the issue of the fibreglass diffused into the environment and the type of dusts generated by the sanding practice. Infusion processes solve these issues at least partially.
There is then the complex matter of scraps and wastes and of the final destination of moulds, they too of plastic reinforced with fibreglass, once ended their service life. The latter are themes not adequately and completely faced, yet, according to the general European provisions (“Sustainable Consumption and Production”) that recommend the need of designing and manufacturing in compliance with LCA (Life Cycle Assessment) and the carbon footprint (ISO/TS 14067).
What of, how is it disposed?
The theme is complex and not organically faced. Various are the disposal modalities: demolition, partial selection and final mechanical treatment or transport to permanent landfills or to heat treatment centres. I know that in the past various projects tried to face the theme, I mention just three of them, as an example: “District of Tigullio boating: Development of a design idea for the collection, the disposal and the recycling of materials deriving from machining wastes and the scrapping of vessels (UniFi Department of Engineering and of Industrial Technologies –EDIT)” “ GeRISNaM Integrated and Sustainable Management of Wastes for the Marche Boating sector of VTR vessels (CNM-Marche Naval Consortium)” “Maritime National Technological Platform Disposal of VTR vessels at the end of the lifecycle (Area Science Park Ts and Mi Polytechnics)”. I think that today it is necessary to revise the theme urgently, in a broad vision of recovery, with a reconversion project (recycling and not only disposal) of the product-good at the life end and introducing the already mentioned LCA criterion for the new implementations (and designs).
What are the existing alternatives?
It is necessary to adopt for the field, with decision, a strategy today summarized by the word sustainability, with the European Community playing a role of strong promotion, with the orientations, the recommendations and the co-financing calls for research and development. The manufacturers of raw materials (for a longer time) and some engineers and shipyards (with caution or perhaps excessive prudence) have undertaken this course, too. I mention vegetal fibres (bio-fibres) and biopolymers for the first, while I recall the design of experimental boats in composite, with basalt fibres and vegetal fibres, for instance the flax fibre, for the second.
Why have you mentioned the flax?
Among vegetal fibres, it is deemed a novelty by designers and shipyards, looking at it with interest as the one with the best prospects and adequate industrial presuppositions. The latter must grant: quality, quantity and constancy of characteristics; user friendliness and expertise of treatments in the productive cycle and for texturing; more in general, it must feature sustainability requisites since the initial product. Among the prospects, it is worth mentioning: the specific performances (for instance the resiliency, the resistance to impact), which introduce engineering novelties in the array of reinforcement materials for composites. Performances due to its typical morphology, the easy impregnation with biopolymers and thermoplastic polymers (matrices) thanks to the expertise in surface treatments, the minor chemical risk of the vegetal fibre compared to the mineral one. Finally, the low specific weight.
How can it be used?
In an attentive design course, flax fibre reinforcements (mat, fabrics, unidirectional, prepregs, …) must be used for the specific properties they show, in the formulations of hybrid multilayer composites, for instance carbon-flax, with requisites of lightness, resistance to impacts and vibrations, of structural elements well designed and positioned.
What actions are advisable to diffuse this material?
Promoting the use of a new material in the shipbuilding sector means to diffuse the knowledge of its performances and testing its suitability through the specific requisites for the design and realization of a vessel. In the last five years, numerous scientific studies on the use of flax fibre as reinforcement (and then as composite in combination with polymeric matrices, also biopolymers) have been published in specialized reviews. However, we need a more specific and targeted testing activity for the assessment of shipping requisites (carried out for instance by an equipped laboratory) and further in-depth engineering study with sector designers.
What is the opinion of Registers of Shipping?
I have a first-hand knowledge of RINA’s will and capability of pursuing innovative researches for the shipbuilding and marine sectors. I really believe that also Registers of Shipping can be interpreters in favour of the use of flax fibre reinforcements for the technological development of the marine field.
What can hinder it on the market?
A typically commercial and simplistic, from the engineering point of view, approach to the use of the new material.
Are market researches still useful?
As already said, the producers of fibres and reinforcements (textured, unidirectional, laminates, prepregs) must collaborate, acknowledging the specific requirements of the boating industry, and concretely support applied research and suitability tests. Besides, they should adapt their production to the needs and approved specifications.
Are there other interesting applications outside the sector?
The automotive industry uses flax fibres as reinforcements in various components and this happens, more in general, in the handling ambit, where lightness and sustainable development are properties and criteria immediately adopted.
I underline that in JEK, 2010 and 2011 editions, products (a prototype vessel for the Mini Transat Racing Boat as well) that have used flax fibre composites were protagonists of the Innovation Award.