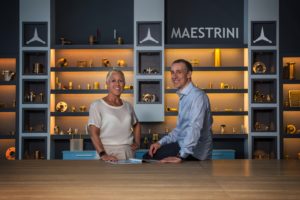
From the idea to the finished product. This, in short, is the activity of Maestrini, a company strongly oriented towards innovation, attention to quality and the continuous research for new solutions to offer. Ingredients that have allowed it to consolidate a role of reference in the national and international quality fittings and nautical items market.
The best fitting on the market, supplied in the shortest possible time. This has always been the main aim of Giulio Maestrini, founder of the Maestrini company formed in 1964 in Quarona, in the province of Vercelli, in a small factory where it started craft production of brass fittings for the local market. A clear and well-defined philosophy which right from the start meant the constant growth in the number of customers, with prestige names added. By the 1980s the fittings spread throughout Italy and production was transferred to a new and larger site where the first transfer machines were used for mechanical processes. In the following years the company began production of strainers, fittings and specific items for yachting, but 1990 was the year of the breakthrough when Maestrini’s children Ivan and Manuela joined the company.
“The company,” says Ivan Maestrini, “got a marketing structure and began to make itself known outside Italy, at the same time speeding up production by using automatic machines in addition to the first CNC lathe.”
Equally decisive was the introduction of CAD/CAM systems which meant that all equipment could be produced internally, permitting further diversification of products still based on the distinctive high quality typical of craftsmanship. Innovation and tradition that led to a large increase in production volumes that quickly required the transfer to a new site, still in Quarona.
“A new site of 4000 m²,” says Maestrini, “which later became the current 7000 m² with the acquisition of new production spaces and the construction of the new office building and the new warehouse of 1500 m².”
Total control of production
After more than 50 years of activity today the company can count on an advanced and evolved technological infrastructure, coordinated and managed by a staff of about 30 spread over the design, administration and production departments. “Even the moulds and all the production equipment,” says Maestrini, “are designed and produced internally to shorten as much as possible the time needed to move from the idea to the finished product.”
Total control of production that makes it possible to obtain for each individual item quality without compromises. And it could not be otherwise, given the broad range of products (which today numbers more than 4000 items), all with specifications that mean they cannot be manufactured on a single kind of machine tool. So the production unit uses automatic CNC lathes for small details, numerically controlled transfer machines for medium-sized pieces and numerically controlled work centres for large elements. There are also automatic multi-spindle machines for mass production and normal CNC lathes for smaller runs. Items can thus be produced from bars, pressings or fusion, but never from diecasting. Attention to the process and also to the raw materials, which are fully traceable so that the element produced can guarantee the specifications required. The company specialises in working with copper alloys, in particular bronze and brass.
“For standard production,” says Maestrini, “we use brass in CW617N, CB753S and CB754S alloys, DZR brass CW602N and CB752S and CB491K bronze. But we can also work with other alloys if customers ask for it.”
Every year Maestrini uses more than 500 tonnes of copper alloys: brass, bronze and DZR brass. This latter, thanks to careful processing and specific heat treatment applied internally, has excellent resistance to corrosion in all uses and is the fastest-growing sector of the company.
Standard or special, but always quality
As mentioned earlier, there are more than 4000 items in the catalogue, in addition to custom production designed and made to precise specifications. The range is basically subdivided into fittings, accessories, strainers and flanges. “In diameters,” says Maestrini, “that can go from 1/8” to 6”, and up to 8” for the strainers. Available in various materials, standard brass, anticorrosion brass and bronze. So there is a wide choice that makes it possible for customers to have as many options as possible even for a single product. We work both with the original shipyards and with retrofitting workshops, with requirements that can often be very different.”
In the case of all products (designed and made using CAD/CAM systems) particular attention is paid to long life. To ensure this, careful oversizing, great strength and greater thickness in the points under most stress are typical of Maestrini production.
“Before going into production,” says Maestrini, “each new item undergoes tests that are far tougher than those it will face in its working life, to ensure perfect working. Here the design and production departments are in close contact so there is complete correspondence between the project and the object. Further added value comes from the meticulous checks carried out during the entire production process and by an internal testing laboratory. This uses not only spectrometers to verify the composition of items and their correspondence with the certificates of the material supplier but, among other instruments and equipment, it also has a test bench for strainers of a diameter of up to 5 inches.”
The test bench has allowed the company to study in depth, validate and propose a migration towards bronze strainers with baskets in polypropylene instead of the more traditional stainless steel. These strainers up to 4 inches in diameter are proving very successful, since they undoubtedly last much longer. Constant requests from customers for larger diameters have convinced the design office to carry out feasibility studies to meet this need.
Increasingly competitive to overcome new market challenges
Quality of processes and products, consolidated since 2003 with ISO 9001 certification, in addition to certifications for specific products: type approval for water strainers from RINA and Dvgw certification for fittings in brass and DZR brass for use with drinking water and gas.
“Since the company was founded,” says Maestrini, “our aim has always been to offer quality products in the shortest possible time. A range of standard solutions that was constantly enlarged, in addition to specific custom products developed in co-design with the customer. All this with total control of the process, from design to the complete working cycle, including the moulds and equipment used, to our precise specification from highly qualified suppliers. I must underline that our partners receive precise indications also on casting materials, traced by us as they enter and leave to guarantee total quality.”
A precise, accurate and scrupulous approach that has imposed, and still imposes, commitment in terms of resources and investments. But it has allowed the company to continue to grow and consolidated over time its proactive, leading role in the national and international markets (today about 70% of turnover comes from exports).
“Growing,” says Maestrini, “means continuing to develop products, sometimes even anticipating market requirements to meet the new challenges and ensure the highest level of competitiveness.”
Interview by Gianandrea Mazzola