The current carbon fiber producers are less than a dozen around the world and operate in (almost) total secrecy. Notwithstanding that, in this article we will do our best to give some information relating to the production process of this incredibly useful material
Marine industry is very much increasing the use of CFRP, due to its outstanding qualities. There is a lot of talk about carbon fibers, but its production is a topic not much under the limelights because it is complex and expensive.
Nonetheless, understanding how carbon fiber is produced can help not only to improve how the material is used, but also to understand the future outlook and prospects for the carbon fiber market.
Carbon fiber: the most relevant details
Carbon fiber is a long, thin strand of material about 0.0002-0.0004 in (0.005-0.010 mm) in diameter and composed mostly of carbon atoms bonded together in microscopic crystals that are more or less aligned parallel to the long axis of the fiber. It is used to produce a large diversity of composites, i.e. materials built up of two or more components.
Its main features are:
- high mechanical resistance;
- low density;
- a very low coefficient of thermic expansion;
- resistance to the effects of several chemical agents;
- good fireproof properties.
Carbon fibres are divided into two main categories, PAN fibers and PITCH fibers:
- PAN fibers are characterized by high resistance and toughness. Tensile strength up to 7000 MPa, Young modulus = 230-600 GPa;
- PITCH fibers are characterized by very high modulus but low resistance. Tensile strength up to 3400 MPa, Young modulus up to 930 GPa.
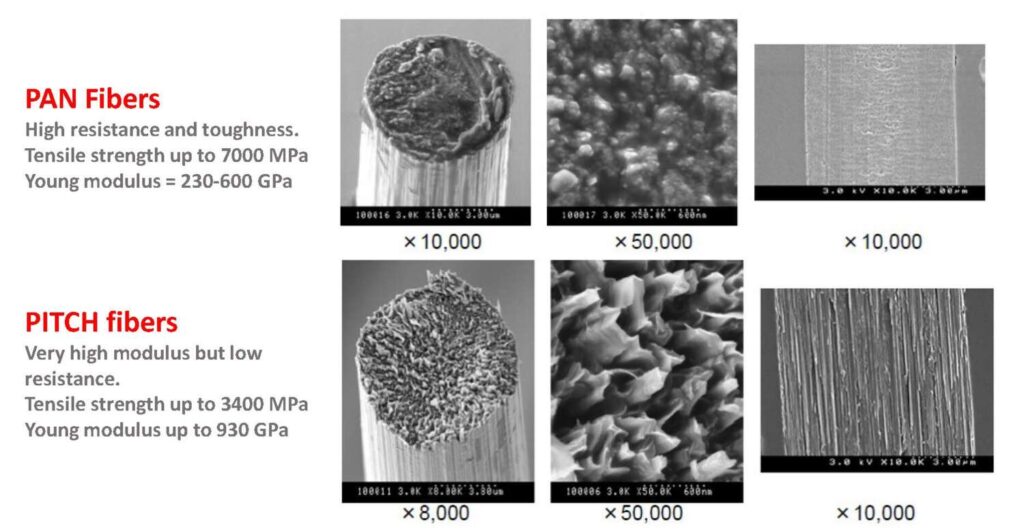
A fundamental difference
Unlike metals, which are homogeneous and – by design – have properties that comply with established standards (for example, each manufacturer’s P20 steel is interchangeable with that of others), composite materials are heterogeneous.
Being made combining different materials (fiber and resin), their variability and therefore their customization are central to their appeal. As a result, carbon fiber manufacturers produce similar but not identical products.
Carbon fiber varies in tensile modulus (or stiffness determined as strain under stress) and resistance to traction, compression, and fatigue. PAN-based carbon fiber is now available in:
- low modulus (less than 32 million lbf/in² or <32 Msi);
- standard modulus (33 to 36 Msi);
- intermediate modulus (40 to 50 Msi);
- high (from 50 to 70 Msi);
- ultra-low modulus (from 70 to 140 Msi).
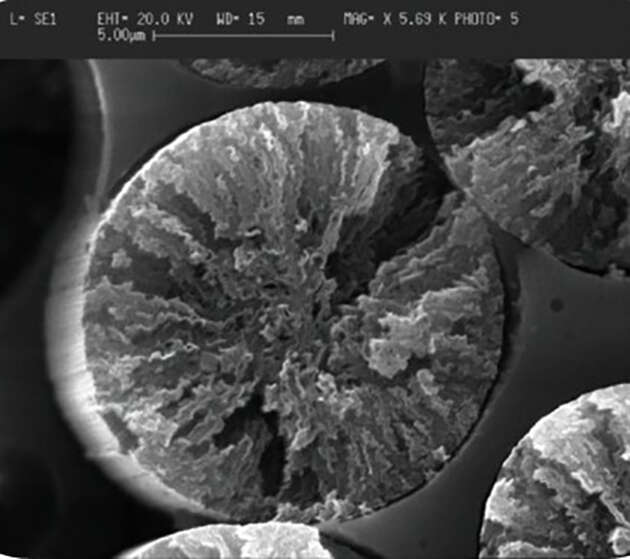
The fiber, available in bundles called “tow”, is available in different sizes from 1K to 350K (1K is equivalent to 1,000 filaments with a diameter of 5 to 10 microns). The products also vary in the degree of carbon content and the type of surface treatment/coating.
The inherent complexity of carbon fiber composites is what adds value to structures made of carbon fiber, because they offer ten times the strength of steel at half the weight.
Carbon fiber is produced by pyrolysis of an organic precursor fiber in an inert atmosphere at temperatures above 982°C / 1800°F. Manufacturing of carbon fiber, however, is a complex undertaking. Throughout the process, tight tolerances define the ultimate usefulness of the fiber, i.e. its future sector of use: to make aircraft and spacecraft parts, racing car bodies, tennis rackets, bicycle frames, fishing rods, automobiles, boats and many other components where light weight and high strength are needed.
The conversion of PAN to carbon fiber has challenged manufacturers for many years; most of a carbon fiber manufacturer’s investment is spent on the precursor. The attention to the precursor’s quality, which the quality of the finished fiber is directly dependent on, minimizes the variation in the yield or the length per unit of weight of the fiber.
Generally, the precursor formulation begins with an acrylonitrile monomer, which is combined in a reactor with plasticized acrylic comonomers and a catalyst such as itaconic acid, dioxide sulfuric acid, sulfuric acid, or methylacrylic acid.
Continuous agitation mixes the ingredients, ensures consistency and purity and initiates the formation of free radicals within the molecular structure of the acrylonitrile. This change leads to polymerization, the chemical process that creates long-chain polymers that can be formed into acrylic fibers. The details of the polymerization are not made available by the manufacturers, but generally the polymerization should reach at least 85% acrylonitrile content.
After washing and drying, the acrylonitrile – now in powder form– is dissolved in organic or aqueous solvents. Organic solvents help avoid contamination by tracing metal ions that could compromise thermal oxidative stability during processing and delay high temperature performance in the finished fiber. The choice of solvent and the degree to which the viscosity of the substance can be controlled (by extensive filtration) are critical to the success of the next step: the formation of the fiber.
This relatively gelatinous and brittle fiber is then washed, coagulated, dried and stretched to continue orienting the PAN polymer. Here, the external shape of the filament and the internal cross section are determined by the degree to which the selected solvent and coagulant have penetrated the precursor fiber, the amount of tension applied, and the elongation rate of the filament (which can be up to twelve times the initial flexibility of the precursor fiber).
An alternative to wet spinning is a hybrid process called “dry jet/wet spinning“, which creates a smooth, rounded fiber that can improve the fiber/resin matrix interface in composite materials.
The last step in the formation of the PAN precursor fibers is the application of a finishing oil to prevent the sticky filaments from clumping together. The white PAN fiber is then dried again and wound onto coils.
Before entering the first oven, the PAN fibers are flattened into a towing band or sheet called warp. The temperature of the oxidation ovens ranges from 200/300°C (=392/572°F). The process combines the oxygen molecules from the air with the fibers in the warp and causes the polymer chains to cross-link. This increases the density of the fiber from ~ 1.18 g/cc up to 1.38 g/cc.
To avoid exothermicity (=total exothermic energy released during oxidation, which poses a real fire hazard), oven manufacturers use a variety of types of airflow to help dissipate heat and control temperature. The oxidation time varies, determined by specific chemical precursors.
In the end, the oxidized (stabilized) PAN fiber contains about 50-65% of carbon molecules, with the equilibrium a mixture of hydrogen, nitrogen and oxygen.
In the absence of oxygen, only non-carbonaceous molecules – including elements of hydrogen cyanide and other VOCs (generated during stabilization at concentration levels of 40 to 80 ppm) – and particulates (such as local accumulation of fiber debris) are removed and exhausted from the furnace for post-treatment in an environmentally controlled incinerator.
Although the terms “carbon” and “graphite” are often used interchangeably, the former indicates carbonized fibers at around 1315°C/2400°F and which contain 93 to 95% carbon. The latter refers to fibers that are graphitized at 1900°C and 2480°C (3450°F to 4500°F) and contain over 99% elemental carbon.
In general, just to give an idea of the temperatures, carbonization begins in a low temperature oven which subjects the fiber to 700/800°C and ends in a high temperature oven from 1200/1500°C. Fiber tensioning must be continued throughout the production process.
Ultimately, the crystallization of carbon molecules can be optimized to produce a finished fiber that contains over 90% carbon.
The number of ovens is determined by the desired modulus in the carbon fiber. Part of the relatively high cost of high and ultra high modulus carbon fiber is due to the length of dwell time and the temperatures that must be achieved in the high temperature furnace. Carbonized fiber loses weight and volume, contracts 5 to 10% in length and shrinks in diameter. In fact, considerably less material comes out of the process.
Treating the surface and sizing
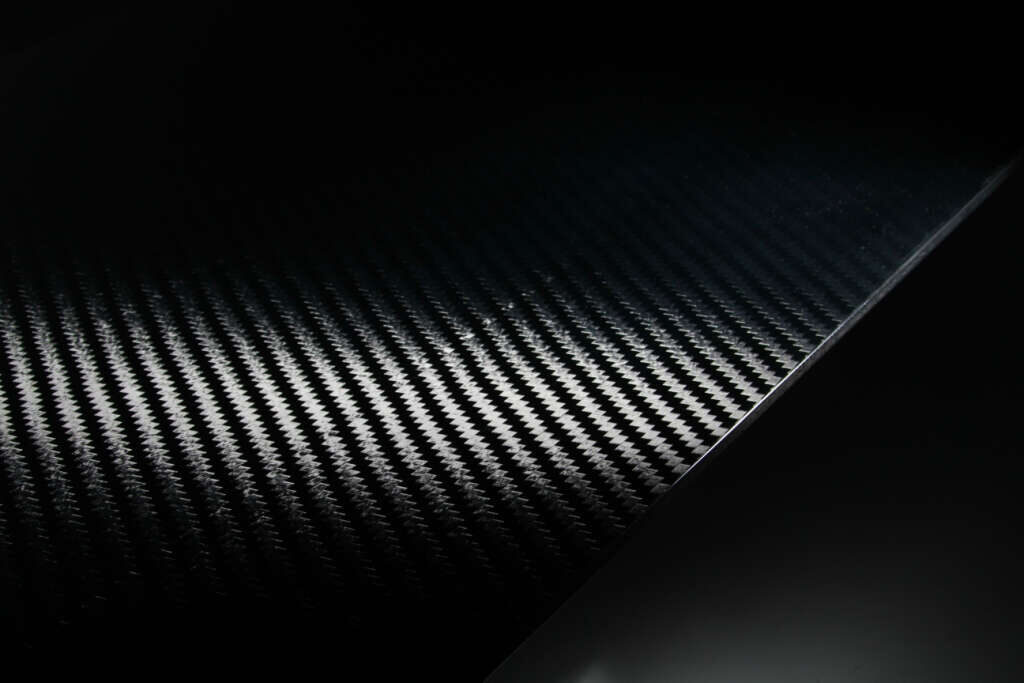
The next step is critical to fiber performance and, apart from the precursor, it makes a supplier’s product more distinct from a competitor’s one. The adhesion between matrix resin and carbon fiber is essential in a reinforced composite; during the production of carbon fiber, a surface treatment is performed to improve this adhesion.
Manufacturers use different treatments, but a common method is to pull the fiber through an electrochemical or electrolytic bath that contains solutions such as sodium hypochlorite or nitric acid. These materials etch or roughen the surface of each filament, which increases the surface area available for interfacial fiber/matrix bonding and adds reactive chemical groups, such as carboxylic acids.
Next, a coating called “sizing” is applied: it protects the carbon fiber during handling and processing (for example, weaving) in intermediate forms, such as dry fabric and prepreg. The sizing also holds the filaments together in individual trailers to reduce fuzz, improve processability and increase the interfacial shear strength between the fiber and the matrix resin.
Carbon fiber manufacturers increasingly use a sizing with the desired specifications in the appropriate composite for the customer’s end use. The crystal alignment makes the fiber incredibly strong for its size. Several thousand carbon fibers are twisted together to form a yarn, which may be used by itself or woven into a fabric. The yarn or fabric is combined with epoxy and wound or molded into shape to form various composite materials. Forty years of processing perfection have brought technological maturity and the ability to translate superior performance and application versatility through fibers to advanced composite materials.
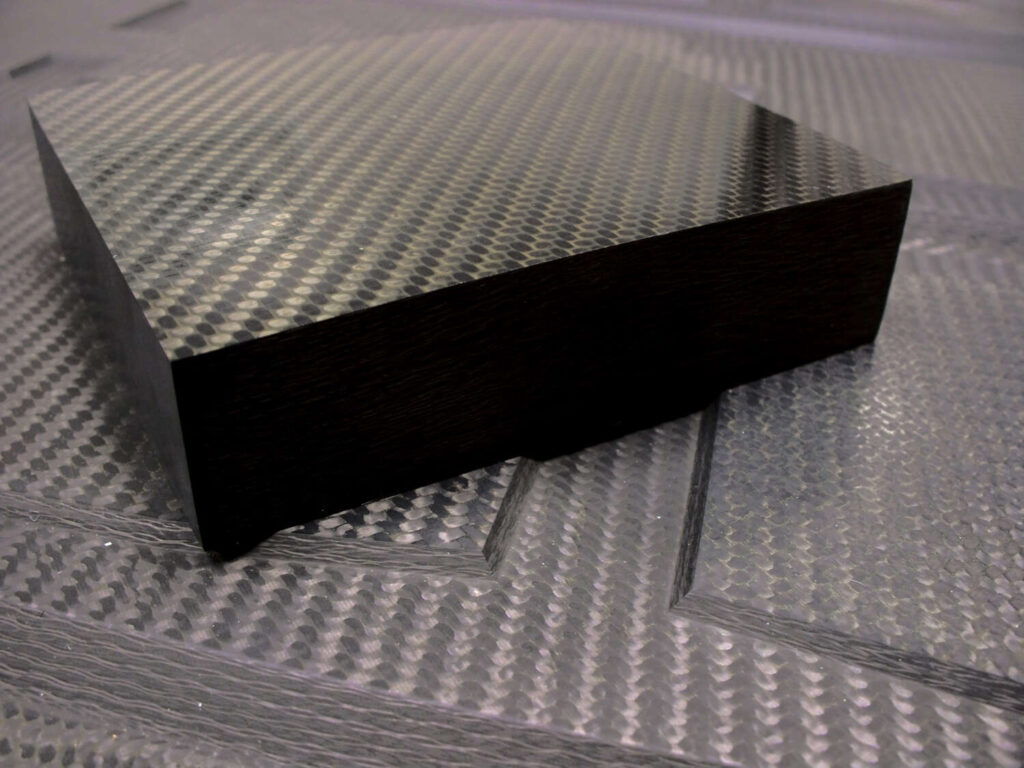
Trends in carbon fiber production
Technological changes have made carbon fiber available and more practical for use by OEMs in a wide range of markets and applications. The surveyors and suppliers who build the kilns and furnaces with which the pyrolysis was carried out have recently outlined some of the most significant developments.
1. Sizing for many matrices
Since most carbon fiber has historically been used with epoxy matrices, the sizing is predominantly epoxy-based and low molecular weight to promote flexibility and spreadability of the fibers. However, research is underway to create chemical sizing to accommodate the variety of matrix resins currently required for end-use applications.
2. More efficient new generation ovens
In the production of carbon fiber, much depends on the design of the ovens that pyrolyze the fibers.
In the oxidation process, the furnace airflow plays a fundamental role in controlling the temperatures of the process and preventing exothermic reactions. Airflow models can be single flow (parallel or perpendicular or multipath). Three important elements are required by carbon fiber manufacturers for oxidation furnaces: productivity, scalability and energy efficiency. The newer generation of larger furnace systems is more efficient, producing a larger volume of carbon fiber with lower energy costs.
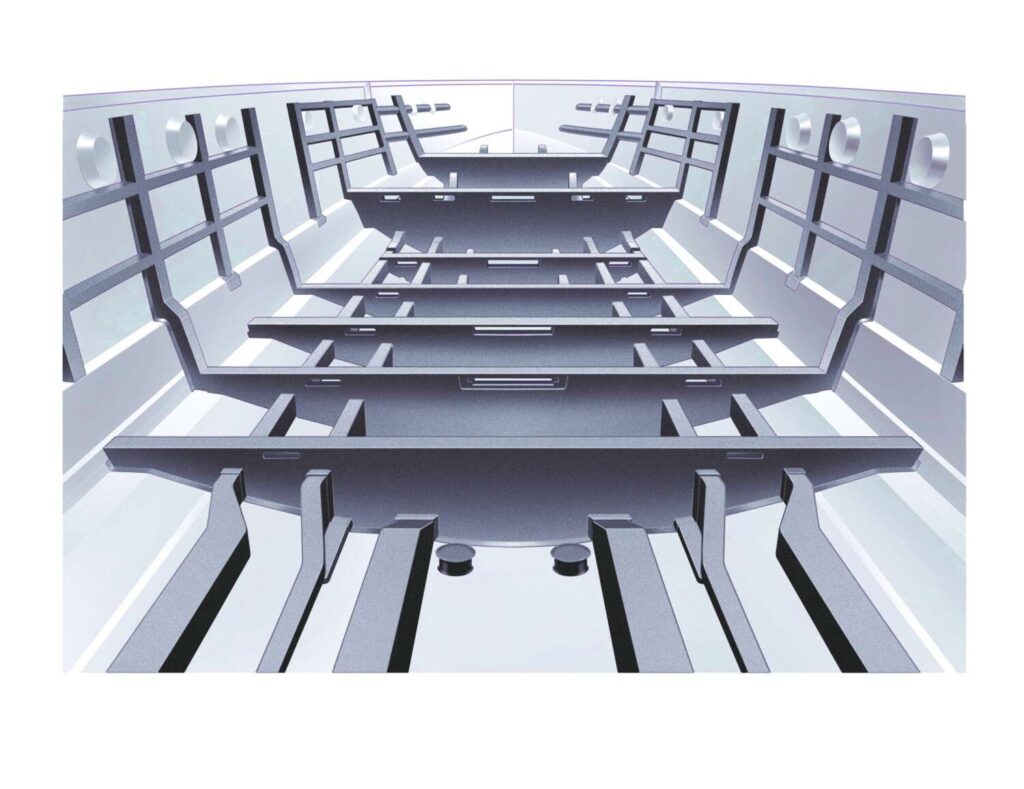