Eliche Radice, with over 100 years of experience, relies on state-of-the-art machinery and software for 100% in-house production. Specializing in custom solutions and complete propulsion systems, the company designs and manufactures propellers and components for boats up to 100m in length.
Technological innovation and industrialization drive Eliche Radice’s business. Positioned as a leader in propellers and propulsion systems for boats up to 100m in length, the company excels in designing, manufacturing, and marketing individual parts while specializing in tailor-made propulsion systems. These comprehensive packages are fine-tuned by a team of engineers in collaboration with shipyards and owners during the boat’s design phases.
According to Luca Radice, CEO of the company, their involvement in developing propulsion systems begins when shipyards select engines. From there, they utilize all elements to design systems tailored to achieve specific goals such as speed, noise reduction, stability, and efficiency. This process involves utilizing 3D-Cad software and culminates in sea trials to ensure optimal performance.
Industrializing propellers
“Without being too presumptuous, I believe that Eliche Radice is today perhaps not the most technological company ever, but certainly among the most technological companies in our field,” says Luca Radice. “For the manufacture of niche products such as ours, we apply the latest mechanical engineering technologies available on the market—a choice that has made it possible to achieve a total degree of industrialization. As one of our friends and competitors says, ‘Eliche Radice are the ones who industrialized propellers.’ We use industrial robots, 3-, 5-, and 7-axis CNC machines that allow us to do numerically important production of both standard and custom parts.”
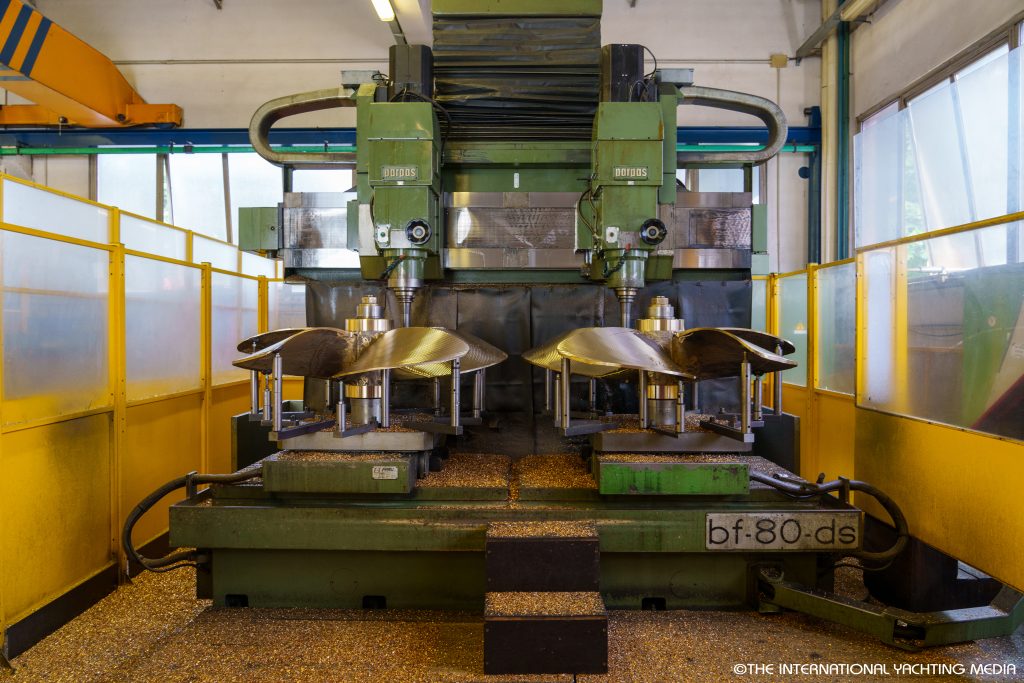
Technological strength The machines and robots in the company optimize machining processes, produce parts quickly and with maximum precision, and ensure high repeatability of a product within certain tolerances and characteristics. “Thinking about the needs of large groups, for us to make 20 axis lines all the same is not a problem. Moreover, few companies can make, for example, axles up to 12m long and beyond with large diameters. And not only that: once the axis is made, our CNC lathes with a motorized turret allow us—unlike other competitors—to avoid having to move and reposition it on other machines for subsequent machining such as making holes, pegs, threadings, etc”.
The same goes for rudders, which come out of plants already complete without having to be moved to milling machines, etc. Complete automation also for the various steps of propeller production: the only manual step is positioning on the balancing machine to perform dynamic balancing, which all Radice propellers have. “We use advanced machinery so much that many competitors rely on us to study special or complicated solutions or to get the finished component”
Innovation and investment
“The world is evolving; it is essential to keep up with it. Let’s say that every year we allocate at least 1 million euros to investments in innovation, then there are special years, such as 2019 when we built the Telgate foundry”.
An investment of 14 million euros for a state-of-the-art foundry with a production capacity of 600 tons, state-of-the-art control systems, and making Eliche Radice the only company in Europe to have the complete resin casting (shell molding) cycle. “This year we will invest in human resources – we are about 100 in the company – to be included in the Technical Department; it is time to make a qualitative leap at the organizational level to project Eliche Radice into the future for the next 100 years”.
In-house processing The main strength lies in the fact that all processing is done in-house (the company depends on outsiders only for the supply of raw materials). “This allows us to have quality controls at all stages of processing and to detect and correct any problems before the parts move on to the next stage. It also allows us to follow customers with special needs and manage deliveries promptly”.
The quest for efficiency Fixed and folding propellers, tractive or propulsive, blades and hubs for variable pitch propellers, inverter coupling flanges, rudders, and bushings, fixed or directional nozzles, propeller shafts and their supports: the products made by Eliche Radice cover the nautical world at 360°, from small pleasure boats to megayachts, from military patrol boats to submarines, from ferries and steamers to tugboats. “By choice, we go up to boats around 100m in length, because it is necessary to give ourselves limits. Today, the world of propellers and propulsion systems is constantly evolving, noise levels within certain parameters and machining of parts to precise tolerances must be ensured. We are able to industrially make propellers from 200 up to 3,500mm in diameter; the limit is the weight, in the foundry we have a casting capacity that reaches a maximum of 6 tons. Theoretically, we could also make larger propellers, up to 4,000mm in diameter, but it would open up issues related to occupational safety, which is always at the forefront with us”.
Materials
Regarding the materials used, except for the shaft lines which are standardized in nautical steel, Eliche Radice uses an in-house designed alloy of nickel, chromium, and aluminum: Mibral. “It has a mechanical strength that exceeds 75kg/mm2: so, it’s a very strong alloy, more than steel, if you consider that the other alloys normally used provide strengths of 60kg/mm2. Mibral allows us to reduce thicknesses and thus increase efficiency.”