Used in the building industry, Kelvet in combination with polypropylene has a low weight and high strength: very interesting characteristics also for the nautical sector
.
Surfcrest engineer Maria di Filippo came up with the idea of creating complex geometry structures through an industrial process, using Kelvet in combination with polypropylene.
As an alternative to GRP composite products, an equivalent model with more attractive characteristics can be obtained because it is lighter, disposable, and eco-friendly. This combination had already been used for architectural finishes, formwork, furniture, bulkheads, panels, and so on.
Such methodology was applied in the nautical sector thanks to the combination of Surfcrest’s technologies and the genius of Vincenzo Catarsi, creator of successful hulls.
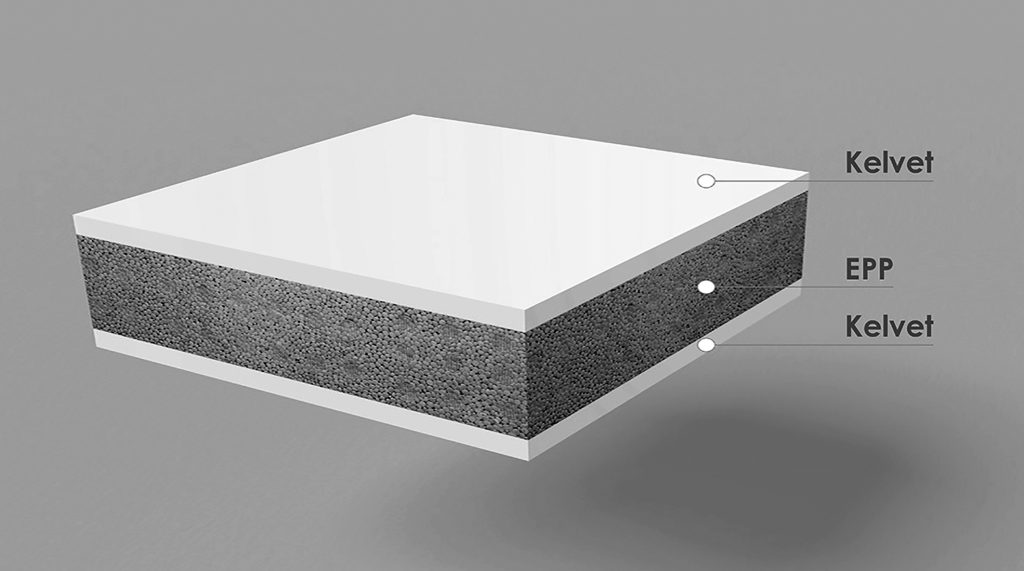
The polypropylene core is millable: the volume of the hull is obtained by subtraction from the solid using five-axis robotic milling machines, so there is no need for a mold to shape a boat.
Next, the covering of the core is made with the Kelvet, a kind of resin that gives it strength and rigidity. Kelvet provides excellent mechanical, weathering, and salinity resistance properties; it also allows painting for different types of surface and color finishes on the hull.
Paradoxically, some shipyards are happily using Kelvet + polypropylene technology precisely to make high-quality female molds suitable for laminating hulls with classic composite materials.
Wide variety of uses and pairings
This type of construction is perfect for small, open boats, but its evolution, also in structural terms, does not exclude more complex, larger constructions. Hull structures up to 7 m in length can thus be made. For hulls between 7 and 13 m in length, sizing them with polypropylene and/or wood fibers is possible.
A peculiarity of the Kelvet technology is the wide variety of uses and great compatibility with other materials (e.g., concrete, stone, steel, wood, glass, plastic, and chemical and mechanical fastener fibers). It is possible, therefore, to combine the polypropylene core of the hull with some steel or carbon structural parts to further strengthen a boat.
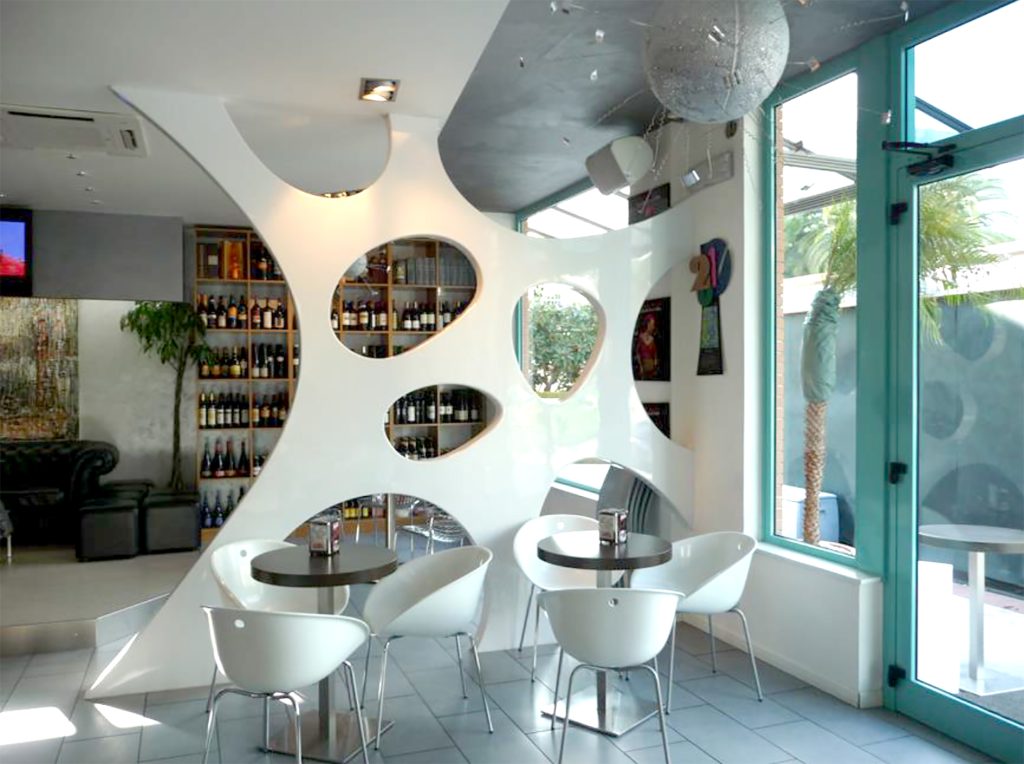
Maximum morphological flexibility
Shapes obtained by milling polypropylene blocks can be extremely articulate and organic. 3D modeling using software allows the project maximum morphological freedom, as opposed to conventional building materials such as metal and wood, which are usually limited in their form from the start.
The ability to have a customizable design for ship constructions – the designer can easily modify the 3D model on the computer according to the customer’s needs without additional costs, as would be the case with the use of a mold – makes the whole process fast, flexible, and cost-effective as well. The peculiar finish of Kelvet also has undoubted aesthetic value.
Unsinkability and ease of repair
A magnificent quality of a hull built with this technology is its unsinkability. In addition, Kelvet is an easy-to-repair material: cracks and impact damage can be remedied relatively easily, without reducing the mechanical performance of the structure. Compared with steel, for which part of the structure must be cut and replaced, professionals can repair the new material locally.
Its low hygroscopicity makes it particularly suitable for applications in marine environments or places with moisture or condensation. The structure is closed-cell and prevents water and moisture from entering the core, increasing its weight and ruining its mechanical performance.
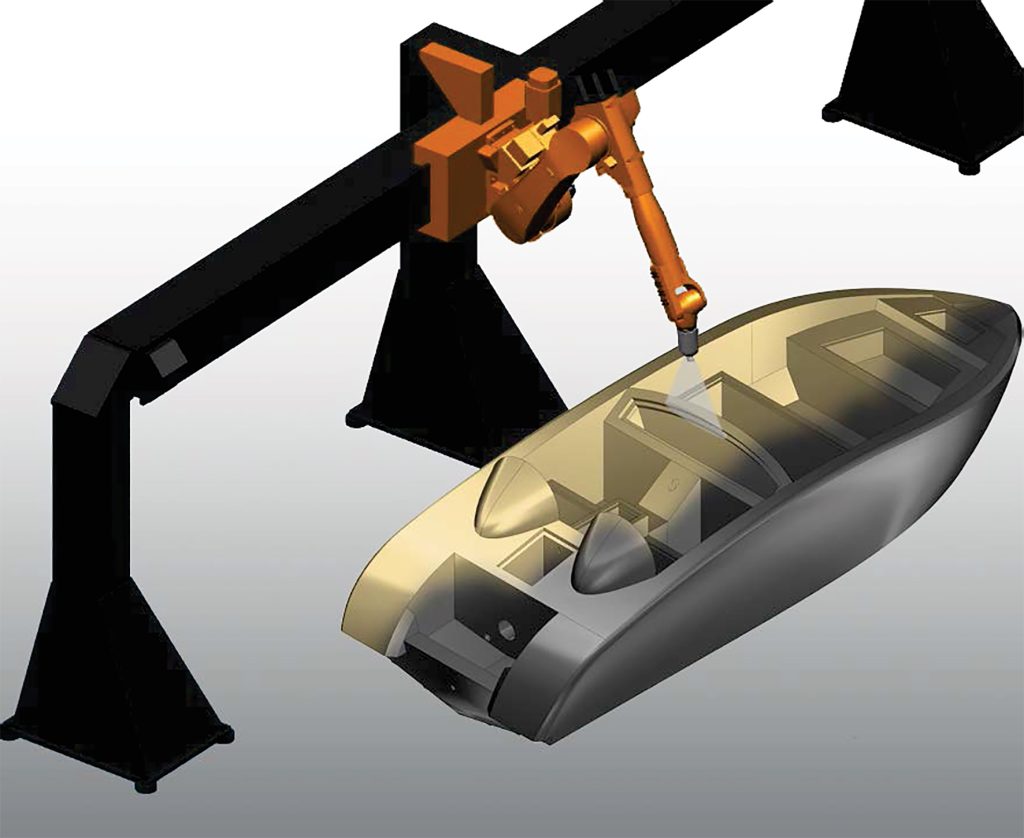
Other properties
The cellular structure of the polymer material, with its microcavities, can inhibit heat transfer: this could be of great benefit in applications where thermal insulation is important. The structure’s closed cells also have a good ability to isolate/absorb sound, a valuable feature when, in the presence of loud noise sources, indoor comfort is to be improved.
Some basic materials in the core have excellent dielectric properties: this means that they do not interfere with radio waves, for example, which is an extremely appreciable feature in boats.
Ecology and sustainability
The combination of polypropylene + Kelvet makes it possible to reduce hull weight, and, therefore, fuel consumption, engine power, and CO2 emissions. In addition, it is an industrial technology and uses a process that does not harm workers’ health or the environment.
The material can be recycled without incurring major disposal costs or shredded without any drawbacks and ‘drowned’ in concrete in place of expanded clay.