The UK’s National Composites Center (NCC) supports the establishment of a new consortium of the country’s leading marine companies, with the challenge of achieving decarbonisation by recycling the composite materials of the maritime industry.
The plan is to build the UK’s first reuse plant for glass fiber reinforced plastics (GRP) and other fibers (FRP). Composites to be used for new components of boats, caravans, wind turbine blades.
Academic research centers and local authorities are also called upon to join the Blue Composites Project consortium. The goal is to jointly tackle the transition of maritime transport towards the zero emissions goal by 2050.
The NCC estimates the presence of six million boats in the European Union (EU) alone, 98% of which are made of fiberglass. Each year, about 1-2% of these boats (between 60,000 and 120,000) reach the end of their life. But only about 2 thousand of these are recycled to date: the recovery of their components is still an expensive activity.
The technology for the recycling of GRP composites
The International Marine Organization estimates about 55,000 tons of GRP composite waste produced each year by the maritime sector: a number that is expected to increase by 10% per year.
To facilitate the recycling of these components, the Blue Composites consortium relies on DEECOM technology, developed by the British company B&M Longworth and originally designed to remove waste polymers from plastic filters and production equipment.
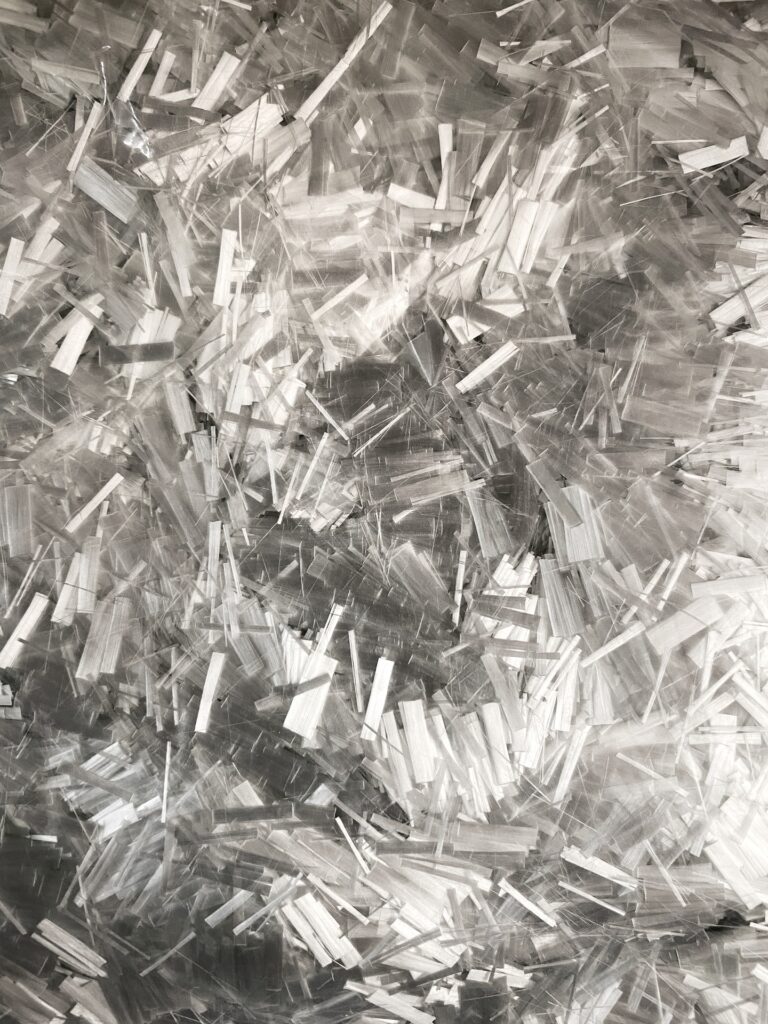
Will Grocott, Chief Surface Transportation National Composites Center said:
“The NCC is working with a number of organizations to find sustainable solutions for end-of-life composites, their associated manufacturing material and consumer waste. We have the knowledge and skills to drive decarbonisation in the composites industry and all sectors in general. Together, we need to become smarter, making sure the next generation of high-performance composite products enable a cleaner and greener future for all of us. ”
The DEECOM process uses pressurized, superheated steam to penetrate microscopic cracks in the composite polymer. After decompression, it expands, breaking down the polymer and carrying away the broken particles.
The pressure swing cycle is repeated until all the matrix is separated from the fiber. With this technology, in partnership with B&M Longworth and the British Cygnet Texkimp, the NCC has recently successfully recovered the carbon fibers from a fully pressure vessel.